Insights & Updates
.webp)
How Advanced Technology is Revolutionizing the Auto Parts Supply Chain
The auto parts supply chain is at a turning point. As the industry grows increasingly complex, technology is emerging as the key to streamlining operations, reducing costs, and meeting the rising demands of customers. From artificial intelligence (AI) to real-time tracking, advanced technology is revolutionizing how businesses manage their supply chains.
In this blog, we’ll explore the transformative impact of these technologies, highlight the benefits they bring, and showcase how APX is leveraging innovation to deliver superior results.
The Growing Role of Technology in Supply Chain Management
AI Integration is Delivering Immediate ROI
Artificial intelligence is no longer a futuristic concept; it’s a critical tool in modern supply chain management. Today, 76% of supply chain leaders have integrated AI into their operations and are seeing immediate returns on investment. From predictive analytics to automated decision-making, AI optimizes processes and reduces inefficiencies.
Real-Time Tracking Boosts Efficiency
Real-time tracking systems are reshaping how businesses manage shipments. By providing full visibility into the movement of goods, these systems reduce delivery delays by up to 25% and significantly improve customer satisfaction. In a competitive market like auto parts, where timeliness is critical, this technology is a game-changer.
Key Technologies Driving Change in the Auto Parts Supply Chain
1. Artificial Intelligence (AI) and Machine Learning
AI is revolutionizing the auto parts supply chain by enabling smarter decision-making. For example:
- Demand Forecasting: AI analyzes historical data and market trends to predict future demand, reducing overstocking and stockouts.
- Predictive Maintenance: Machine learning algorithms monitor fleet performance and flag potential issues before they lead to breakdowns, minimizing downtime.
2. Fleet Management Systems
Advanced fleet management systems optimize routing, track fuel consumption, and monitor driver performance. These systems:
- Reduce operational costs by identifying the most efficient delivery routes.
- Improve safety and compliance by monitoring driver behavior in real time.
- Ensure timely deliveries, which is critical in the fast-paced auto parts industry.
3. Real-Time Tracking and Visibility
Real-time tracking offers end-to-end visibility into shipments, allowing businesses to:
- Monitor the exact location of goods throughout the supply chain.
- Anticipate and address delays proactively, ensuring on-time delivery.
- Enhance customer trust by providing accurate updates on shipment status.
How APX is Leading the Way with Technology
At APX, we understand that the future of logistics lies in technology. That’s why we’ve integrated cutting-edge solutions into our operations to provide our clients with unmatched service.
1. Route Optimization
Using AI-driven fleet management systems, APX optimizes delivery routes to reduce fuel consumption and ensure faster, more reliable deliveries.
2. Real-Time Tracking
Our real-time tracking tools give clients complete visibility into their shipments, offering peace of mind and proactive problem-solving capabilities.
3. Predictive Analytics
APX leverages predictive analytics to anticipate supply chain disruptions and develop contingency plans, keeping your operations running smoothly.
4. Data-Driven Insights
We provide clients with actionable insights to improve decision-making and streamline logistics processes, ensuring a competitive edge in the auto parts supply chain.
The Benefits of Partnering with APX
By integrating advanced technology into our logistics solutions, APX helps auto parts businesses:
- Reduce Costs: Streamline operations and optimize resources with AI-powered tools.
- Improve Efficiency: Deliver consistent results with real-time tracking and route optimization.
- Enhance Customer Satisfaction: Ensure timely deliveries and transparent communication with end-to-end visibility.
- Scale Operations: Leverage our technology to adapt to market demands and grow your business seamlessly.
Schedule a Demo of APX's Fleet Management Technology
Ready to see how APX can transform your supply chain operations?
Schedule a demo today to explore our advanced fleet management systems, real-time tracking tools, and AI-driven solutions. Discover how we can help you achieve operational excellence and meet the demands of the evolving auto parts market.
.webp)
Sustainability in Auto Parts Logistics: How Going Green is Also Cutting Costs
Sustainability is no longer a buzzword in the logistics industry—it’s a business imperative. Auto parts suppliers are recognizing that adopting sustainable practices not only reduces environmental impact but also drives significant cost savings. By integrating eco-friendly solutions into logistics operations, companies can achieve greater efficiency, improve customer satisfaction, and contribute to a greener future.
In this blog, we’ll explore the dual benefits of sustainability in auto parts logistics and showcase how APX is leading the way with innovative, green logistics solutions.
The Financial and Environmental Case for Sustainability
1. Cost Savings Through Route Optimization
Companies incorporating sustainable practices, such as route optimization and reduced idle time, have seen a 15% reduction in logistics costs. Efficient routing minimizes fuel consumption, shortens delivery times, and lowers overall transportation expenses—all while reducing carbon emissions.
2. The Circular Economy Advantage
Circular economy principles—recycling, reusing, and reducing waste—are transforming logistics operations. These practices are projected to save $4.5 trillion globally by 2030, offering a clear financial incentive for businesses to embrace sustainability.
Sustainability Trends in Auto Parts Logistics
1. Rising Demand for Green Logistics Solutions
Consumers and businesses alike are increasingly prioritizing sustainability. Auto parts suppliers are under pressure to adopt green logistics practices, from eco-friendly packaging to low-emission transportation methods.
2. Regulatory Compliance
Stricter environmental regulations are prompting businesses to adopt sustainable practices to avoid penalties and maintain compliance. Logistics providers that meet or exceed these standards gain a competitive edge in the market.
3. Customer Expectations
Clients are seeking logistics partners that align with their sustainability goals. Offering green solutions not only attracts environmentally conscious customers but also enhances brand reputation.
APX’s Commitment to Sustainable Logistics
At APX, we understand that sustainability is key to the future of logistics. That’s why we’ve developed comprehensive eco-friendly initiatives to support our clients’ sustainability goals while delivering exceptional results.
1. Emission Reduction Through Route Optimization
Using advanced fleet management systems, APX optimizes delivery routes to reduce fuel consumption and minimize emissions. By cutting down on unnecessary mileage and idle time, we help clients achieve both cost savings and environmental benefits.
2. Eco-Friendly Fleet Practices
Our fleet incorporates energy-efficient vehicles and low-emission technologies to ensure environmentally responsible transportation. We’re committed to continually upgrading our fleet to meet the highest sustainability standards.
3. Waste Reduction with Circular Logistics
APX promotes circular economy principles by streamlining reverse logistics processes. From recycling used auto parts to reusing packaging materials, we help clients minimize waste and reduce costs.
4. Transparent Reporting
We provide clients with detailed sustainability reports, showcasing the environmental impact of their logistics operations. These insights empower businesses to make data-driven decisions that align with their sustainability goals.
Why Sustainability Matters for Auto Parts Suppliers
1. Stay Competitive in a Changing Market
Sustainability is no longer optional; it’s a requirement for businesses aiming to remain competitive in today’s market. Customers and partners are seeking environmentally responsible solutions, and those who fail to adapt risk being left behind.
2. Achieve Long-Term Cost Savings
Sustainable practices like route optimization, waste reduction, and energy-efficient transportation are proven to lower logistics costs. By partnering with a forward-thinking provider like APX, auto parts suppliers can achieve immediate and long-term financial benefits.
3. Enhance Brand Reputation
Companies that demonstrate a commitment to sustainability build stronger relationships with customers, employees, and stakeholders. A green logistics strategy is not just good for the planet—it’s good for business.
Take the First Step Toward Sustainable Logistics
APX is proud to lead the way in sustainable logistics for the auto parts supply chain. With our advanced technologies, eco-friendly fleet practices, and commitment to reducing emissions, we help businesses achieve their sustainability goals while cutting costs.
Ready to Go Green and Save?
Consult with APX to explore eco-friendly logistics solutions tailored to your needs. Let us show you how sustainability can drive efficiency, reduce costs, and future-proof your business.
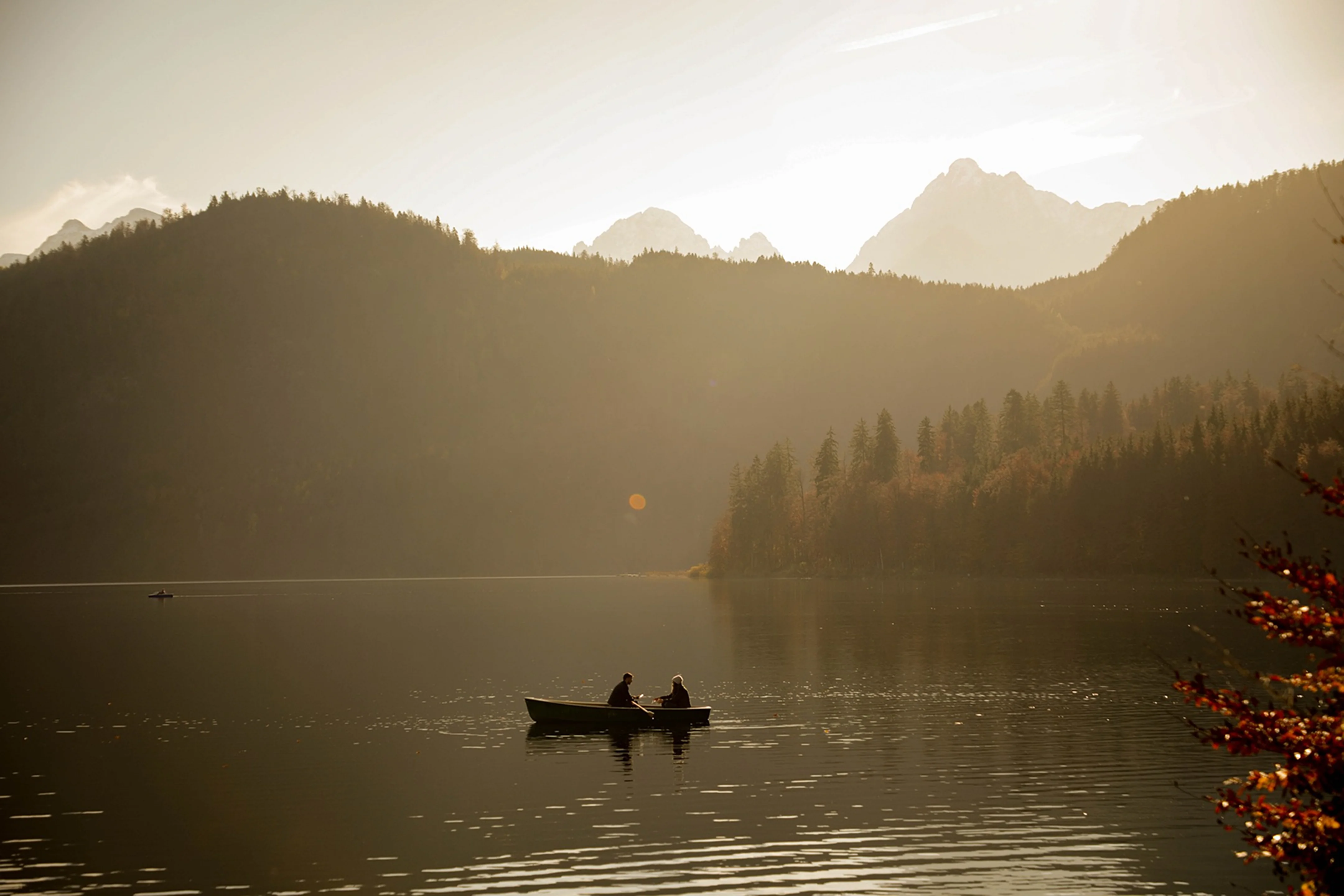
The Untapped Opportunities in Electric Vehicle (EV) Logistics: What Auto Parts Suppliers Need to Know
The rapid rise of electric vehicles (EVs) is not just reshaping the automotive industry—it’s transforming the logistics landscape as well. For auto parts suppliers, this shift presents unprecedented opportunities and challenges. The ability to adapt logistics operations to meet the unique demands of EV components will determine which companies thrive in this evolving market.
In this blog, we explore the untapped opportunities in EV logistics and how APX is positioned as a forward-thinking partner to help auto parts suppliers succeed.
The Growing Demand for EV Logistics Solutions
The EV Market Is Accelerating
The U.S. electric vehicle market is growing at an unprecedented pace, with the number of EV manufacturing plants set to increase from 9 to 41 by 2029. This dramatic expansion reflects a broader shift toward local sourcing and domestic production.
Additionally, the Department of Energy has committed $755 million toward the construction of a synthetic graphite factory in Tennessee to support EV battery production. These investments underscore the need for robust supply chain solutions capable of managing specialized EV components.
Unique Challenges in EV Logistics
While the opportunities are significant, EV logistics also come with unique challenges:
1. Battery Handling and Transportation
EV batteries are large, heavy, and hazardous. Their transportation requires compliance with strict regulations, specialized equipment, and proper handling to ensure safety and minimize risks.
2. Specialized Routing
Given the size and weight of EV components, including batteries and drivetrains, logistics companies must optimize routing to reduce costs and ensure timely deliveries. This requires advanced fleet management systems and data-driven routing strategies.
3. Just-in-Time (JIT) Delivery
To maintain efficiency, EV manufacturers increasingly rely on just-in-time delivery models. This requires precise scheduling, real-time tracking, and seamless coordination across the supply chain.
4. Sustainability Requirements
As EV manufacturers prioritize sustainability, they expect logistics partners to implement eco-friendly practices, including reducing emissions and utilizing energy-efficient transportation methods.
How APX Is Leading the Charge in EV Logistics
APX is at the forefront of addressing these challenges with innovative solutions tailored to the unique needs of the EV supply chain. Here’s how we’re setting the standard:
1. Expertise in Battery Logistics
APX offers comprehensive services for handling and transporting EV batteries. Our team is trained in regulatory compliance, ensuring safe and efficient delivery of hazardous materials.
2. Customizable Delivery Options
With flexible solutions, APX provides tailored delivery options to meet specific client needs, including same-day or time-sensitive deliveries. Whether you’re shipping individual components or full truckloads, we’ve got you covered.
3. Advanced Fleet Management
Our state-of-the-art fleet management system optimizes routing, minimizes delays, and ensures cost-effective transportation. Real-time tracking offers complete visibility into your shipments, giving you peace of mind.
4. Sustainability Commitment
APX integrates sustainability into every aspect of its logistics operations. From energy-efficient vehicles to optimized delivery routes that reduce fuel consumption, we help clients align with green initiatives.
The Opportunity for Auto Parts Suppliers
For auto parts suppliers, aligning with the EV revolution is no longer optional—it’s a necessity. By partnering with APX, you gain access to:
- Industry Expertise: Leverage our knowledge of EV logistics to navigate regulatory requirements and market demands.
- Streamlined Operations: Focus on your core business while we handle the complexities of EV supply chain management.
- Scalable Solutions: Adapt to the growing EV market with logistics solutions that scale with your needs.
Take the Next Step with APX
The EV market is growing, and so are the opportunities for auto parts suppliers. Don’t let logistics challenges hold your business back. APX is here to help you navigate the complexities of EV logistics with ease and efficiency.
Schedule Your Free EV Logistics Assessment
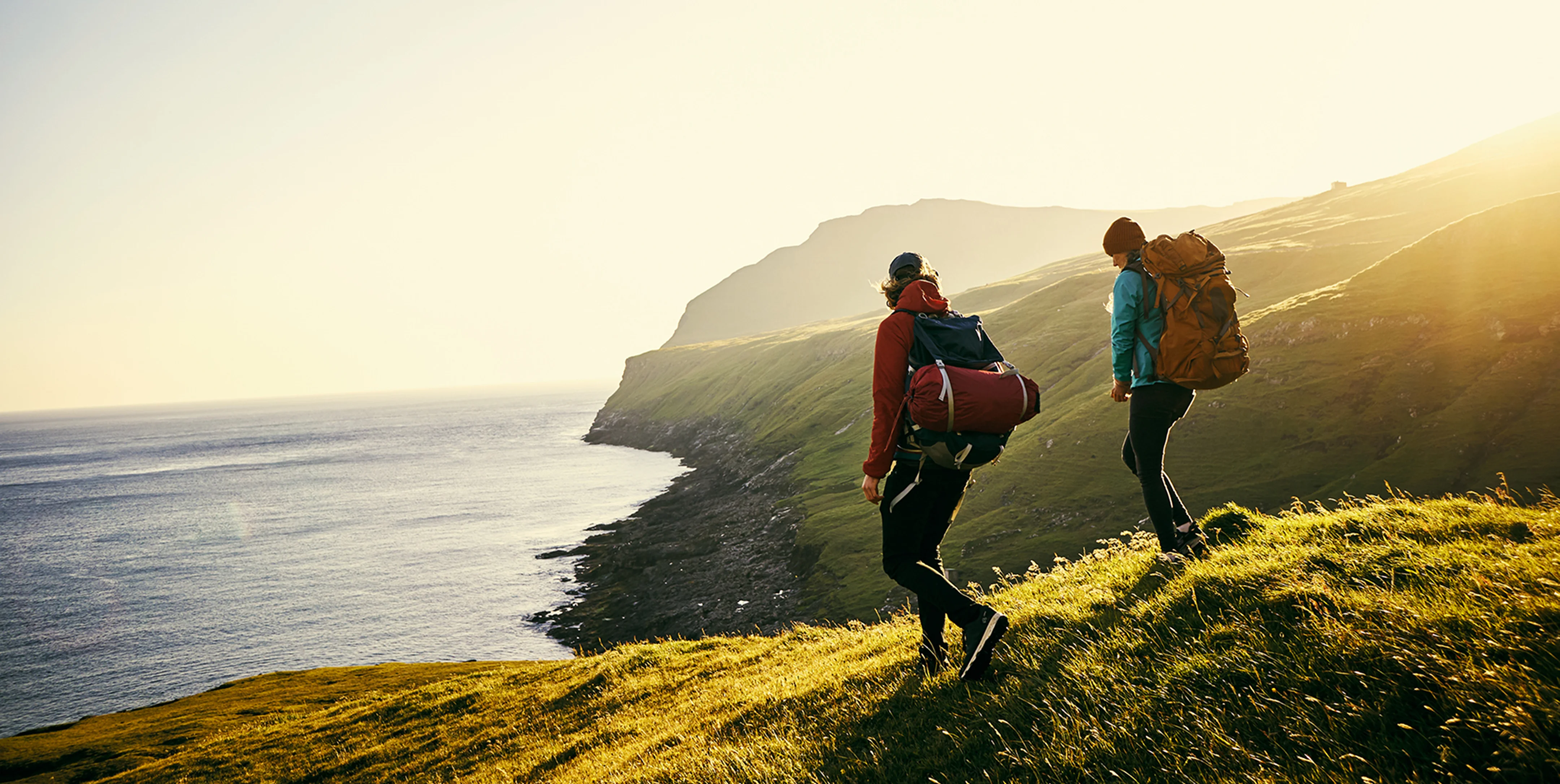
Why Managing an In-House Fleet Is Costing Auto Parts Businesses More Than They Realize
The auto parts supply chain is an intricate and highly competitive industry where every dollar counts. Yet, many businesses unknowingly bleed cash due to inefficiencies in managing their in-house fleets. While it may seem like keeping logistics internal provides control, the hidden costs often outweigh the perceived benefits.
This blog explores why in-house fleet management is costing auto parts businesses more than they realize, highlights key inefficiencies, and offers a better alternative for streamlining operations.
The Hidden Costs of In-House Fleet Management
1. Rising Logistics Inefficiencies
Studies show that 15-20% of small and mid-sized businesses' logistics costs stem from inefficiencies in fleet management. These include delays caused by vehicle breakdowns, absentee drivers, and unpredictable fuel price fluctuations. For businesses operating in the fast-paced auto parts supply chain, such inefficiencies can result in missed deadlines, dissatisfied customers, and increased operational expenses.
2. Maintenance and Repair Costs
Owning and maintaining a fleet means shouldering significant upkeep costs. Auto parts businesses must budget for regular vehicle maintenance, unexpected repairs, and compliance with safety regulations. When vehicles are idle due to repairs, the lost productivity further compounds expenses.
3. Absenteeism and Labor Management
Absenteeism among drivers is another costly challenge. Finding replacement drivers at short notice disrupts schedules, increasing overtime pay or requiring last-minute hires. These issues strain resources and detract from your focus on core operations like sourcing, inventory management, and customer service.
4. Quality Assurance and Counterfeit Parts
Counterfeit auto parts, including critical components like airbags, are increasingly entering the market. Businesses often face additional quality assurance costs to mitigate the risks associated with substandard components. While not directly tied to fleet management, these costs are exacerbated when logistics delays lead to supply chain bottlenecks.
Why Outsourcing Logistics Is the Solution
Outsourcing logistics to a professional third-party provider can eliminate many of these inefficiencies, offering businesses a more predictable and cost-effective solution.
1. Flat-Rate Pricing for Budget Control
Outsourcing allows businesses to benefit from flat-rate pricing, which eliminates surprises like fluctuating fuel costs and unexpected maintenance expenses. With a predictable logistics budget, businesses can allocate resources more efficiently.
2. Access to Advanced Technology
Third-party logistics providers often leverage advanced technologies such as fleet management systems and real-time tracking. These tools optimize routing, reduce fuel consumption, and improve delivery reliability, giving businesses a competitive edge.
3. Reduced Operational Burden
By outsourcing logistics, auto parts businesses can redirect their focus from managing drivers and vehicles to strategic initiatives like expanding market reach and enhancing customer satisfaction. Professional providers handle the logistics headaches, ensuring seamless operations without requiring constant oversight.
4. Mitigating Risk and Improving Service Quality
Outsourced providers often have established networks and contingency plans to handle disruptions like absentee drivers or vehicle breakdowns. This ensures consistent service quality and timely deliveries, reducing reputational risks for auto parts businesses.
Take the First Step Toward Streamlined Logistics
Managing an in-house fleet might feel like a necessity, but for many auto parts businesses, it’s a costly inefficiency. By outsourcing logistics, you gain access to advanced solutions, predictable pricing, and the freedom to focus on your core business.
Schedule a Complimentary Logistics Cost Assessment Today
Discover how much your business can save by identifying inefficiencies in your current operations. Our experts will provide actionable insights and a customized plan to optimize your supply chain.